Last week, I went over the definition of Lean manufacturing and Ergonomics. But now, I want to dive deeper and explain some of the core principles of lean manufacturing. While these philosophies are applied most in a manual assembly environment, they can be used in plenty of different settings and life practices. Even better, you can implement many of these concepts today and start becoming more efficient with your processes. Let's dive right in with principle number one...
Jump to Section:
1. Minimize Excess Motion
2. Reduce Inventory
3. Organization
4. Flexibility
5. Consistency
Lean Manufacturing Principles
1: Minimize Excess Motion
Minimizing excess movements and motions is the core principle behind Lean. Wasted motion brings no value to the manufacturer or consumer, so why keep it? A Lean process has what is called "continuous flow." Workcells employing continuous flow usually have a "U" shape, but they can also be a straight line if necessary. The shape helps material flow from one ergonomic workstation to the next, with each station designed specifically for the task at hand. This process has become invaluable as consumers continue to desire customizable products, making many operations high-mix/low-volume productions, meaning they offer a few products that can be configured in many different ways.
Conveyors and/or rollers are often used to move materials from one station to the next, and ball roller platforms can be used to help things move along smoothly. Carts, generic or custom-built for the application, can also help with material movement, and don't forget about Electric Case Lifters (The automatic sensors make all the difference)! These all aid in minimizing excess motion of both the handler and material. Look out for my next blog post to go into more detail about specific accessories for your workstations!
2: Reduce Inventory
Workstations should maintain the right amount of materials to continue production without excess (no overproduction). This will look different for each application, but the goal is to decrease replenishment intervals and travel time between tasks. Storage should be as close as possible to where it will be used and in a designated storage system that is visual and easy to see at a glance (like color-coding). Properly storing your materials helps avoid long downtimes and wasted efforts, and helps reduce necessary floor space for processes.
Storage systems can be custom-designed as well. Flow rack systems are effective, extremely modular, and reduce inventory space and material cost. Flow racks leverage gravity to make replenishment easy when it's needed, and they're easily extendable and convertible so they can change with you. An application of this would look like an assembler at their station removing an empty bin of parts from the shelf, then having a full bin of those same parts roll down behind it to replace that spot on the rack (like a soda machine). Maybe our fictional organization aims to have enough full bins of pieces lined up behind one another to run through each shift without refilling any stations. Then, each station can refill their pieces at once at the end of their shift in an orderly and efficient manner, maximizing everyone's time.
3: Organization
Organization serves many of the same purposes of reducing inventory, like taking up less space and time, but refers more to the micro-layout of each workstation than to the macro-work cell. Everything in front of an operator should be well thought out and displayed in an order that makes sense, and each tool should have a designated place. Walk through the steps the operator will take, and organize what is used most to be closest to them. Minimize the distances between parts that need to be put together, use labels, and make sure everything is readily available; otherwise, people will waste time sifting through things to find what they need. It's human nature. A clean and organized work environment promotes a culture of safety and responsibility, and research has shown that people are more efficient in an organized environment. One added benefit of using aluminum extrusion workstations is their clean design, requiring little upkeep or maintenance to keep work areas looking new.
4: Flexibility
Flexibility is imperative for any Lean design. Processes can't grow when they aren't flexible. As product lines change, so do adaptable stations. Aluminum extrusion is the material used in all the pictures in this article, and this material makes each station extremely adaptable and reusable as things change and grow. It is lightweight and doesn't require welding, using only basic hand tools for all assembly. If you want to learn more about why aluminum extrusion is the perfect flexible material for work cells, we wrote this article on how you can Build Anything with Aluminum Extrusion.
Not only do the workstation components need to be flexible for change, but the workstation itself needs to be flexible for each operator. This calls back to our Ergonomics 101 article, as ergonomics helps each operator maximize their individual efficiency. There are multiple ways that workstations can be engineered to be adjustable, but they will vary with each situation. A good place to start is with adjustable height chairs and tables. Putting monitors and instructions on a swivel helps reduce set-up time between shifts as each operator can quickly and efficiently adjust things to their needs.
5: Consistency
So far, I've focused mostly on how Lean strategies allow you to do more with less, but consistency ensures that high-quality production is still being maintained in a reduced amount of time. Consistency is achieved in many different ways, but it starts with the standardization of processes. Without a standard process, don't expect consistent results. The next step is taking those standard processes and creating clear instructions that are easily visible and readily available. It's also recommended to have designated points at various intervals in a process serve as quality control checkpoints. The continuous flow (U shape) workstation design helps with innate quality control. Each station performs its own simple inspections and tasks, and then moves on to the next station, so problem areas and faulty products are easily spotted.
Summary:
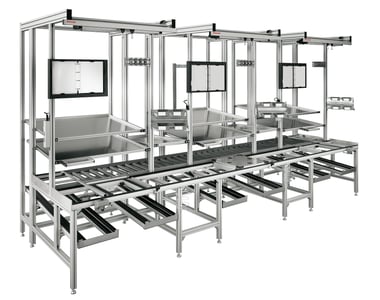
When done right, all of these Lean principles overlap and work together to form an efficient and optimized system that promotes an organized, efficient, and safe environment. Airline Hydraulics specializes in the design, engineering, manufacturing, and installation of simple and complex Lean work cell systems, so contact us with any thoughts or questions wherever you are in your Lean process, we'd love to help.
In my next post, I'll be going over essential accessories every Lean and Ergonomic workstation should have, so don’t forget to subscribe to our blog!
If you have a question or comment about this post, please leave it in the comments below!
Resources and Information:
- Learn more about Lean Work Cells
- Success Story: Lean Work Cell Achieves a 90% Reduction in Production Cycle Time
- Shop Workstations and Accessories
- Technically Speaking - Airline Hydraulics
- Airline Hydraulics YouTube Channel
Contact Us:
Ask your Airline Rep. or contact us for assistance with ordering or customizing an order.
- 800-999-7378
Leave Comment