Packaging processes have long been known for generating some of the highest cost and labor waste in production applications. BUT - It doesn't have to be that way, as more companies are catching on to the heightened efficiency and reduced costs with automated packaging solutions. Lets dive in and also explore a project where we built a tailor-made automated packaging table for a delighted customer.
Video not playing? Watch on YouTube
Jump to a Section
Why Use an Automated Packaging System? | How Automated Packing Systems Work |
Key Tips for Getting Started | Success Story | Summary
Why Use Automated Packaging Systems?
Automated packaging systems have become indispensable for businesses in today's fast-paced world. The advantages they offer are plentiful and can significantly benefit companies. Let's delve into the reasons why these systems are a game-changer for businesses.
1. It Pays for Itself
It's no secret that automation streamlines and speeds up packaging processes, reducing the time needed to package and ship products, but the price of these systems can come with some sticker shock.
Luckily, even with a higher initial cost, automated packaging equipment can pay itself off in as little as eight months to a year. After that, you can fully enjoy significant cost savings and increased efficiency. This is especially true in industries where package-dyeing processes can be automated, resulting in major financial and technical benefits.
2. Improve Product Accuracy and Consistency
Automated systems are designed to perform repetitive tasks with precision, minimizing the risk of errors or inconsistencies in packaging. This ensures that every product is packaged and labeled correctly, meeting any required standards, and enhancing quality control.
Utilizing packaging automation offers multiple avenues for enhancing quality control:
Consistent Sealing ✔
Automated machinery can be programmed to exert uniform pressure during the sealing process, guaranteeing that every package is securely sealed.
Precise Product Verification ✔
Automated packaging systems incorporate sensors capable of verifying the size and shape of each product prior to packaging. This proactive measure minimizes the potential for errors and product damage.
Error-Reducing Labeling ✔
Automated packaging systems are equipped with meticulously programmed print labels and barcodes. This precision significantly lowers the likelihood of errors in labeling and packaging.
3. See up to 80% Reduction in Labor Costs
Automating the packaging process saves businesses on labor expenses and allows employees to redirect their focus toward more valuable and quality-driven tasks. With the potential to save over 80% of manual labor hours, you can optimize your workforce and increase productivity while maintaining high-quality packaging standards.
4. Increase Employee Safety
Have you ever gotten scratched by a tape gun or knicked by a box cutter? Although painful, these injuries are minor compared to some of the more serious accidents and long-term musculoskeletal disorders related to large-scale manual packaging lines. We have first-hand experience witnessing this with our machine safety division, MPSA.
With automated machines handling the bulk of the packaging process, the risk of injuries related to manual handling or repetitive tasks is significantly reduced, creating a safer working environment for employees.
Overall, automated packaging systems offer many benefits, including increased efficiency, improved accuracy, reduced labor costs, and enhanced safety. By implementing these systems, businesses can optimize their packaging operations and gain a competitive edge in the market. Next, check out our success story of an in-depth explanation of a real-world application.
How We Built an Automated Packaging Table
Discover our latest success story, where we created a customized automated packaging table for a valued client facing the challenge of managing their increasing order volumes. Our tailor-made solution provided them with a highly efficient and flexible packaging system to meet their evolving needs.
Watch the video of this table in action!
Our engineering and fabrication team designed and built the automated packaging system with aluminum extrusion as the main structural material of the frame. The advanced technology incorporated includes sensors, pneumatic components, and a control system to allow for easy operation.
The system was designed to handle various product sizes and packaging requirements, offering flexibility and adaptability to the customer's needs. It also integrated seamlessly with the customer's existing warehouse management system, enabling efficient order fulfillment and inventory management.
The outcome increased productivity, reduced labor costs, and enhanced overall efficiency, enabling the customer to meet their growing demand while maintaining high-quality packaging standards.
How Are Automated Packaging Systems Designed?
Automated packaging systems rely on advanced technology and machinery to perform packaging tasks efficiently. These systems typically involve various component pieces working together in a symphony of collaboration. The makeup of the solution entirely depends on the unique needs of the manufacturer, but can typically include:
Conveyors
One of the key components is the conveyor system, which transports products from one station to another during the packaging process.
AGVs
Automated guided vehicles (AGVs) are commonly used in the packaging process to move products along an assembly line, or from one area of the building to another. An Example of an easy-to-use AGV is our little friend here, FRED!
Sensors and Scanners
With advanced sensors and scanners, you can do high-volume quality checks and make split-second decisions on where to send what product down conveyors and different automated processes.
Explore Sensors & Scanners by Omron Automation
Explore Sensors & Scanners by Banner Engineering
Data Collection
Data collection has become necessary for optimizing operations, enhancing efficiency, and ensuring product quality. Industries can make informed decisions, monitor performance, and proactively address challenges by systematically gathering, analyzing, and interpreting data.
Don't collect data? We have scalable options:
Simple & Straightforward
For the fastest way to collect data on manual processes, I recommend SmartMONITOR by WERMA. You can even apply for a risk-free test kit. This solution can get up and running quickly and can give you some immediate and simple feedback on your processes, like uptime and downtime.
Detailed & Thorough Data
To get more in-depth and granular data on your system, I recommend these products by Banner Engineering that can give a higher-level & accurate look into your processes:
1. Snap Signal: A more configurable data-collection option that allows you to collect and analyze data from any sensor (not brand-specific) on your site. Think high-level data to optimize OOE (Overall Operations Effectiveness) and OEE (Overall Equipment Effectiveness).
2. Asset Monitoring Gateway (AMG): A turnkey package for data collection that allows you to collect and analyze data from up to 20 connected sensors. This provides high-level data for OEE (Overall Equipment Effectiveness).
Control Systems
Automated packaging systems often utilize software and control systems to control and coordinate the different components. These systems enable operators to set parameters, monitor the packaging process, and adjust as needed. They also ensure synchronization between the various components, optimizing efficiency and minimizing errors.
Explore Process Control Systems & Components
Robotics
Depending on the complexity of the packaging requirements, automated systems may incorporate additional features, such as robotic arms for handling delicate or intricate products. Properly safeguarded robots can take care of tasks such as filling containers, sealing packages, applying labels, and shrink-wrapping products.
3 Tips for Getting Started with Automated Packaging Systems
To help wrap things up, here are three takeaways to consider when moving forward with automating your packaging process:
Tip #1: Use data as your roadmap
Looking at the bigger picture is great, but it's too daunting and expensive to automate everything simultaneously. So first, collect data to determine the weakest areas of your packaging process - AKA wastes time, energy, labor, or materials. Then, look into those areas, or bring in a consultant like Airline to help automate that area in the most cost-effective way.
For example, if your manual worktables are wasteful, upgrade to ergonomic or semi-automated workcells with conveyors. If your staff is wasting too much time transporting box after box, add an AGV to automate box transportation easily. You'll reap the automation benefits one step at a time.
Tip#2: Flexibility is key.
A good automated system should be able to accommodate various product sizes, shapes, and packaging requirements. It should offer adjustable settings and customizations to meet the specific needs of your products.
The packaging system should also be able to accommodate increased production volumes or additional packaging requirements without significant modifications or upgrades. If a solution only works for today's packaging needs and doesn't have room for tomorrow's, I'd keep looking.
Tip#3: Think of the future with reliability and maintenance.
Reliability is crucial, so look for manufacturers with high-quality components and a proven track record of reliability. This will minimize downtime and ensure consistent performance.
But the system will wear in time, and parts must be serviced. Consider how easy that will be for your team going forward and develop a plan. The system should have a user-friendly interface and intuitive controls that make it easy for operators to set up, operate, and maintain the system.
Additionally, access to technical support and spare parts availability is essential for minimizing disruptions and downtime. It might be a good time to consider adding some predictive maintenance software to make future maintenance even more manageable by being able to plan ahead.
By considering these three tips, you can select an automated packaging system that meets your specific needs and maximizes the benefits for your business.
Airline is Here to Help!
In addition to automated packaging systems, Airline specializes in building a wide range of solutions using aluminum extrusion and advanced automation technology. Contact us today to discuss your project requirements and discover the possibilities.
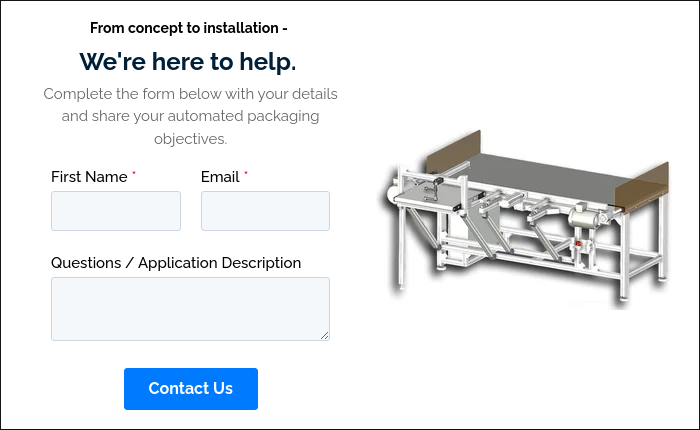
Airline Resources
Leave Comment