Editor’s Note: This blog post was updated in May 2025 (originally published in March 2022) for accuracy and comprehensiveness.
"Safety first” isn’t just a saying; it’s a must when working around machinery. From workshops to manufacturing floors, mechanical hazards are a daily concern. That’s why machine safety devices play such a critical role in protecting people, not just machines. Whether you're dealing with points of operation, power transmission, or moving parts, the right machine safety equipment can help reduce risks and keep people and machines safe.
Common types of machine safety devices, like interlocks, light curtains, and emergency stops, are specifically engineered to address these dangers. But it’s not always easy to know which solution is right for your application; let’s walk through the most common machine safety equipment you’ll find in today’s facilities.
Skip to a Section:
Start with Hazard Identification | Machine Guarding | Safety Interlock Switches | Light Curtains & Laser Scanners | Emergency Stop Buttons & Ropes | Safety Mats, Edges, & Bumpers | Safety Controllers, Relays, & Modules | Trapped Key Interlock Systems | Energy Isolation Equipment | Indicator Lights | Additional Resources
Why Machine Safety Devices Matter: Start with Hazard Identification
The truth is: no two workplaces are the same, and the right machine safety equipment isn’t just about the machinery itself. It’s about how people use it.
That’s why identifying hazards isn’t as simple as checking off a list of devices. You need to understand how your team interacts with the machine — where they stand, how they load parts, what movements they make, and what could go wrong. The risks don’t live in the machine alone; they live in the moment when people and machines meet.
That’s exactly what a machine safety hazard identification is designed to uncover.
At Airline, our machine safety division, MPSA, specializes in risk assessments that factor in real-world human behavior, not just technical specs. If you’re not sure which safety control devices or guarding solutions you need, start with a hazard assessment. It’s the smartest and safest first step you can take.
We offer tiered hazard identification services to match your goals, timeline, and budget:
Safety Survey ($) – Quickly spot the biggest risks and prioritize high-hazard machines.
Risk Assessment ($$) – A thorough analysis that meets ISO-12100, ANSI B11.0, or RIA TR 15 standards.
Risk Assessment & Detailed Scope ($$$) – Includes drawings, corrective actions, and a fixed-price proposal to help you move forward with clarity and control.
Whether you’re trying to reduce unplanned downtime, keep your workers safe, or meet compliance with confidence, our tiered approach gives you the insights and options to take action at your own pace with your budget and resources in mind.
1. Machine Guarding
Machine guarding acts as a physical barrier between a hazard and personnel and is probably the most common machine safety device. Machine Guards come in all shapes and sizes depending on the application but usually consist of an aluminum extrusion or steel frame with a thick, clear polycarbonate or wire mesh barrier. Guards can be custom-built to fit any application, and a benefit to aluminum extrusion guarding is that it's versatile enough to adapt to your application.
2. Safety Interlock Switches
Safety interlock switches are often used in conjunction with machine guarding. When installed on a guarded gate or door, these tamper-resistant switches shut systems down if the door is opened or removed.
|
3. Light Curtains & Laser Scanners
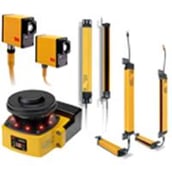
Light curtains and laser scanners both use sensors and beams of light to create invisible barriers around hazards that sense the presence of anything that shouldn't be there. When those sensors are tripped, the hazard is automatically shut off.
Light curtains are bars of sensors and receivers that typically act as an invisible door or passageway, keeping anything that may accidentally pass through the curtain while hazards are active and safe. Light curtains are usually positioned vertically,
Laser scanners send their signals horizontally (perpendicular to the ground) to protect user-designated areas. Safety laser scanners keep everything set at a safe distance away from active hazards, stopping it if something comes too close. Scanners are ideal for complex and irregularly shaped areas not easily solved by other safeguarding solutions.
4. Emergency Stop Buttons & Ropes
Emergency stop buttons and pull systems allow personnel to quickly and effectively stop systems at any time in an instant way. These devices are wired to override all other system controls and remove power. E-stop controls need to be readily available to personnel, so it's likely that you may need more than one, depending on the size of your application.
5. Safety Mats, Edges, & Bumpers
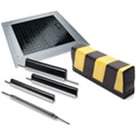
Safety mats, edges, and bumpers are contact-sensing devices that function from pressure sensitivity when touched. A safety mat gives the ability for a machine to only activate a function while a user is standing on it. A safety edge or bumper may halt an automatic door that's closing if pressure or resistance is detected.
6. Safety Controllers, Relays, & Modules
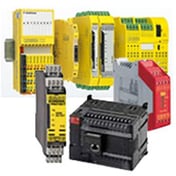
Safety controllers, relays, and modules control many of the other safety devices mentioned in this article. They're the brains of the operation, ensuring safe start and stop functions for hazardous machines. Relays and modules control things like safety light curtains, switches, and safety mats. Safety controllers can often replace multiple safety relay modules in applications that include multiple high-level safety devices and functions.
7. Trapped Key Interlock Systems
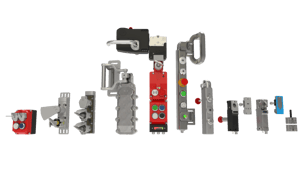
Trapped key interlocks are mechanical safety devices that control access to hazardous machines through a predetermined sequence of key exchanges. One of the most trusted names in this technology is Fortress Safety
These systems work by trapping and releasing keys only when it's safe to do so, ensuring that energy sources are isolated before any access to a machine is allowed. This makes them ideal for industries where safety depends on precise sequencing, such as packaging, food and beverage, metalworking, etc.
Unlike electronic safety systems, trapped key solutions don’t require wiring at the gate, making them a cost-effective retrofit option. They're modular, highly customizable, and are even rated for SIL 3 (EN/IEC 62061), Category 4, and PLe (EN/ISO 13849-1) safety levels, backed by TÜV approval.
8. Energy Isolation Equipment
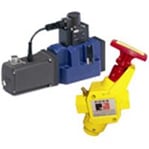
Just because a system is off, doesn't mean it's safe, especially to perform maintenance or be in a compromising position. Unexpected bursts of pneumatic or hydraulic energy can have catastrophic effects, but lockout equipment ensures that all of the potential energy in the system is neutralized for good, preventing any unexpected startups.
9. Indicator Lights
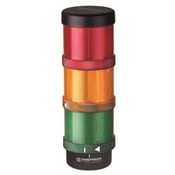
Light and colors are some of the fastest ways to get real-time safety status indications. Lights can be used individually or stacked as a tower, provide high visibility, can be placed inside dangerous areas, and are customizable to signal whatever properties your application requires. Having a red light on while a hazard is active and a green light while inactive is one of the simplest examples of getting instant visual safety feedback.
Machine hazards are real threats, but there are many modern machine safety devices designed to help minimize and eliminate those risks. There is no one-size-fits-all in safety, and the best way to apply these safety devices will vary by the application and industry safety standards.
If you have any questions about which devices are best suited for the safety of your application, reach out to one of our machine safety specialists at MPSA, or you can shop for the listed products below.
Related Articles & Resources
Explore More Machine Safety Articles
Explore MPSA's Machine Safety Website
Contact MPSA
Webinar: Safety Doesn't End at the Wire
Machine Safety Standards & Regulations
Leave Comment