Editor's note: This post has been updated in April 2024 for comprehensiveness.
Whether you're new to machine automation or an industry veteran, IO-Link's implementation and advancement continue to shape the future of our industry. But what exactly is it, and how does it work? In this blog post, we will explore the basics of IO-Link, its capabilities, and its advantages for industrial automation processes. Let's take a closer look at this innovative technology and discover why it's becoming an essential tool for manufacturers worldwide.
Jump to Section:
The Basics | The Biggest Advantages | IO-Link in Practice | How to get started with IO-Link | Resources and Info
🔎 Explore Machine Automation Technologies
Key Takeaways✔️ IO-Link is a standardized protocol (IEC 61131-9) that enables detailed and efficient communication between sensors and actuators in automation systems, offering rapid communication, ease of maintenance, and versatility through various operational modes and the use of standard cables. ✔️ IO-Link facilitates enhanced productivity in industrial settings by enabling predictive maintenance, efficient device configuration, and improved data management. Capabilities like automatic parameter download, remote device reactivation, and diagnostic features lead to more responsive and reliable systems. ✔️ Innovations in IO-Link technology aim to further simplify the integration of devices from various manufacturers into automation systems, as exemplified by tools like the IODDfinder. They also extend the functionality of the system through advancements like IO-Link Wireless and integration with higher-level systems through IO-Link to OPC UA Companion Specification. |
Understanding IO-Link: The Basics
At its core, IO-Link is an industrial communication method used between sensors and actuators, an IO-Link master control unit, and a higher-level controller like an HMI (Human Machine Interface) or PLC (Programmable Logic Controller). It is a short distance (20 meters or less), wired (or wireless), digital, and bi-directional networking standard per IEC standard IEC 61131-9.
The most critical adjective in the above sentence is bi-directional, as IO-Link allows for IO-Link capable sensors and actuators to communicate numerous data points back to the master controller and, ultimately, the user. The end result is a very robust communication system.
IO-link's capabilities far surpass those of legacy systems, offering enhanced control and a wealth of data, from parameters and identification to diagnostics. With IO-Link, the state of the art in device communication is not just about speed, which typically clocks in at around 2.3 ms at COM-2, but also about the depth and richness of the data exchanged.
Previously, devices operating at the field level, like sensors, valves, switches, and encoders, worked in the dark, (hopefully) performing their active duties but not reporting any information back.
However, industry advancements like IIoT (Industrial Internet of Things) and Industry 4.0 (automation and intelligent machines in manufacturing) require abundant, readily available, recordable, and shareable data, and manually collecting all of that data from traditional machines is tedious and cumbersome.
That's where IO-Link steps in as the standard way for field devices and controllers to communicate. It makes it easier to collect, track, and store device data.
The basics of IO-Link configuration
An IO-Link system consists of an IO-Link master with complete access, visibility, and control over every IO-Link-enabled device to which it is connected. The IO-Link master sends and receives data and essentially acts as a middleman between sensors and actuators and the higher-level controller, but not all controllers use the same communication language.
As the network standard, IO-Link integrates with all of the various industrial protocols that PLCs use, such as Ethernet, Profibus, and other Fieldbus networks. IO-Link converters can even bring an analog-type field device into an IO-Link system. Note that IO-Link is not just another Fieldbus but a point-to-point communication protocol. Its open standard can integrate into virtually any Fieldbus or automation system.
What Does IO-Link Look Like In Practice?
The Core Components
At the heart of an IO-Link system lies a trio of essential elements: the controller, the IO-Link master, and the myriad of IO-Link devices they command. Each IO-Link master orchestrates communication with the connected devices and interfaces with a higher-level controller. It also houses parameter data and the IODD (IO Device Description) file.
The IO-Link master, which can be PLC rack cards or standalone devices, is the intermediary that translates the language of fieldbus communications into something IO-Link devices can understand.
Learn more about IO-link components in our blog post: How to Get Started with IO-Link
What devices can an IO-Link master recognize?
👉 IO-link-enabled sensors and actuators
👉 RFID devices
👉 Signal devices and more
Communication Flow
As we mentioned before, bidirectional communication makes IO-link a very robust communication system. The IO-link master and field devices engage in a continuous dialogue that encompasses process data, value status, and detailed device data.
This exchange is not just about the back-and-forth for processing digital signals—it’s a conversation that ensures each device performs at its best, with the IO-link master facilitating the flow of information.
Service protocol data units (SPDUs) are the envelopes that carry the information cargo, delivering everything from basic device details to comprehensive diagnostics and status reports.
The beauty of IO-Link communication lies in its inclusivity. It supports a variety of data types, which reinforces the system’s robustness.
IO-Link communication includes:
✔️ Cyclic data: keeps a steady pulse on the process
✔️ Acyclic data: provides nuanced details that make each operation unique
✔️ Service data: supports system maintenance and diagnostics
✔️ Events: notifies the system of specific occurrences
The Six Biggest Advantages Of IO-Link
1. Data Availability
To run a smooth operation and optimize maintenance and production schedules, you need data. IO-Link provides data routinely and automatically (cyclic data) and commands (acyclic data).
There are three primary types of data that an IO-Link device transmits:
📈 Process Data: Process Data is considered the latest state of the sensor or actuator, such as speed, temperature, distance, etc. It is transmitted cyclically, which means automatically, at regularly defined intervals.
📈 Service Data: Information about the device itself, such as the type of field device, the manufacturer, the operating parameters, serial number, configuration, etc. Also called Device Data
📈 Event Data: These are notifications like error messages and maintenance warnings, often about dirty sensors or overheating. A warning message can be sent acyclically (not scheduled) as events occur.
All of this data is available in real-time for monitoring and recorded over time to analyze trends.
2. Significantly Reduce Unplanned Downtime
Many operations function with broad maintenance routines that become lax and put on the back burner as their list of reactive problems grows. IO-Link provides early warnings and reduces the likelihood of catastrophic failures.
Devices communicate standard or vendor-specific information concerning alarms or informational messages through an event facility, keeping operators apprised of emerging issues. This includes the signaling of device events, such as error messages related to short-circuits or maintenance requirements.
The IO-Link master offers the following features:
👍 Measures and reports the quality of transmission, including telegram retries and communication aborts, back to the control system
❗ Detects and reports any interruption in operation if an IO-Link device is removed, prompting swift corrective action
📈 Provides detailed port status information through advanced diagnostic web pages, aiding in trouble detection and resolution without external technical support.
3. Easy Device Replacement
Because the IO-Link master stores all service data (device data), replacing faulty devices is as easy as plugging them in. Configuring replaced devices no longer requires highly skilled and experienced personnel. The IO-Link master will ensure that the replacement component is the correct replacement and instantly configures to the previous device's specifications.
Even if The "plug and play" and diagnostic/troubleshooting functionalities of IO-Link mean that any downtime event that does occur will quickly recover.
4. Reduced Wiring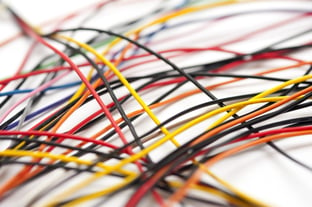
An underrated benefit of IO-Link is that it often simplifies and reduces cabling. In addition, it uses unshielded three or five-wire cables, meaning it is more cost-effective with fewer types of cord sets required.
The advent of IO-Link Wireless marks the next chapter in the evolution of industrial automation, offering the following benefits:
👍 Freedom of wireless network communication between sensors, actuators, and controllers - Say goodbye to the tangling web of wires
👍 Reliability and low latency, matching the deterministic communication of its wired counterpart
👍 Response to process value changes with necessary speed and accuracy
👍 Operation in the unrestricted 2.4 GHz ISM band
👍 Support for up to 40 devices per IO-Link Wireless Master, providing substantial operational capacity without sacrificing performance.
👍 Ease of network expansion, allowing for factory layout changes and machinery modifications with minimal disruption
5. Remote Monitoring and Configuration
IO-Link allows remote monitoring and modification of device parameters through the master control system. In many cases, changes can even happen while the machine is still running! This is invaluable in manufacturing operations with frequent product changeovers (they make many different products), as IO-Link can make transitions between products seamless, saving significant amounts of downtime.
This also means that operations do not need as much skilled staffing on-site, as problems can be identified and resolved from anywhere (especially since technicians no longer need to configure devices).
6. Protecting Your Automation System
Safety is paramount in any automation system, and IO-Link Safety ensures that this principle is upheld with utmost priority. As an extension of the standard IO-Link protocol, IO-Link Safety adds an additional safety communication layer that is approved by TÜV-SÜD and complies with the stringent safety rules of IEC 61508 and ISO 13849.
Functional safety communication protocols like PROFIsafe utilize the Black Channel Principle as a carrier for safety process data and additional safety codes over IO-Link Safety, thus maintaining a consistent communication stream for safety-related devices.
This extended communication reaches both the master and device layers, supporting the integration of any type of field Safety Devices (FS-Devices), from sensors and actuators to complex mechatronics.
The Role of IO-Link in Data Management
As industry standards evolve, so do the expectations for device performance and integration. With IO-Link, users can anticipate a suite of advanced features that enhance overall system performance. The promise of robust configuration and diagnostic settings, manageable through any preferred Fieldbus, eliminates the need for manual tweaking, thereby simplifying system integration.
Furthermore, the functionality and performance of IO-Link masters can be elevated through firmware updates readily available on the manufacturer’s website.
These advancements are not just about keeping pace with technology—they are about setting the stage for a future where the connected IO-Link devices are more than just parts of a machine; they are intelligent components capable of self-optimization and proactive communication.
By leveraging fully digital communication, IO-Link devices offer the following benefits:
👍 Maintains data integrity and accuracy, ensuring that no data is lost, even over extended distances
👍 Enables real-time bidirectional process and diagnostic data transmission
👍 Provides detailed information like temperature readings and error counts
👍 Empowers operators with a comprehensive overview of their systems.
Integrating IO-Link with OPC UA is another leap forward, creating an efficient sensor-to-cloud data flow that enhances data availability and application flexibility. Adopting a JSON-based exchange format exemplifies IO-Link’s seamless integration with IT systems, offering data transport options like MQTT and standardized semantic definitions. This integration ensures that IO-Link data is accessible and presented in a manner that is both comprehensible and actionable, bridging the gap between operational technology (OT) and informational technology (IT).
Remote Device Parameterization
The agility of an IO-Link system is exemplified in its ability to perform remote device parameterization. This feature allows for the modification of device parameters from afar, accessible through user interfaces such as:
👨💻 PLCs
🖥️ HMIs
💻 PCs
📱 Mobile devices
This is done without halting production. In the event of device replacement, the system’s capacity for automatic parameter download minimizes unplanned downtime, swiftly bringing the new device up to speed with its predecessor’s settings.
The acyclic data exchange mode that an IO-Link device supports transmits these updates, enhancing the flexibility and efficiency of managing device configurations. Moreover, device ports can be remotely reset via the IO-Link master, allowing for device reactivation without needing physical intervention—a feature that underscores the protocol’s commitment to efficiency and ease of use.
What Can IO-Link Look Like In Practice?
Let's look at what an IO-Link system does in an everyday setting.
Let's say a traditional photoelectric sensor just failed on a production line.
A failure like this is entirely unpredictable. The sensor functioned adequately and was "routinely checked." Still, because of random factors and unknown deterioration, the failed sensor has shut down the entire line for an undetermined amount of time. It will now take time (which is money in manufacturing) to identify the problem, find which sensor is faulty, replace it, and then appropriately configure it. If the sensor is faulty, potential product defects must be accounted for.
Let's re-imagine this scenario, but instead, with IO-link sensors.
The IO-Link master continuously monitored the condition and performance of any connected IO-Link sensor. As performance metrics are monitored over time, a slow decline in sensor performance was detected (previously "unknown deterioration"). The faulty sensor was scheduled to be checked and/or replaced during routine maintenance procedures, avoiding the stoppage entirely.
Also, when the technicians replaced the faulty sensor, the IO-Link master already had the previous sensor's configuration settings saved, so the new one was instantly correctly integrated.
Innovations in IO-Link: Looking Ahead
The march of progress never halts, and IO-Link technology is no exception. The innovations currently shaping the world of IO-Link are focused on standardizing the integration of devices from multiple manufacturers, thereby simplifying the setup process for users.
A shining example of this effort is the IODDfinder, a centralized database provided by the IO-Link Community that offers easy access to device IODDs, enabling the seamless integration of devices into control programs. This foresight in development signals a future where the complexities of device setup are a thing of the past, and the focus can shift entirely to the optimization and performance of the automation system itself.
IO-Link is the standard communication protocol that helps users get vital information about their machine devices. In addition, IO-Link makes critical data and device controls remotely available and makes maintenance a breeze.
All IO-Link capabilities result in overall reduced costs, improved machine availability, and increased process efficiency. Operations that are severely impacted by unplanned or extended downtimes and/or experience frequent changeovers have the most to gain from IO-Link's advantages. Still, operations of all shapes and sizes can benefit!
Look out for the next IO-Link article, which will talk about essential devices that are IO-Link capable, so don’t forget to subscribe to our blog!
If you have a question or comment about this post, please leave it in the comments below!
Frequently Asked Questions About IO-LinkIs IO-Link Ethernet IP?
|
Resources and Information:
How to Get Started with IO-Link
Technically Speaking - Airline HydraulicsAirline Hydraulics YouTube Channel
Contact Us:
Ask your Airline Rep. or contact us for assistance with ordering or customizing an order.
800-999-7378
Leave Comment