The manufacturing industry is on the brink of a major transformation as the dawn of 2024 approaches. Given the current labor market and technological advancements, machine automation, a powerful change agent, has become an integral part of this industry. This blog post examines the manufacturing industry trends, opportunities, and challenges that we anticipate will shape this sector in the coming year. Stay with us as we delve into the outlook of the manufacturing industry for 2024 and explore the exciting future that automation holds.
Jump to a Section
Swiss-Army-Knife Systems | Labor Shortages | New Applications | Adaptability | Onshoring | Simulation Technology | Vision Systems | Cloud-Based Digital Architecture | Generative AI | Expert Resources | Looking Forward
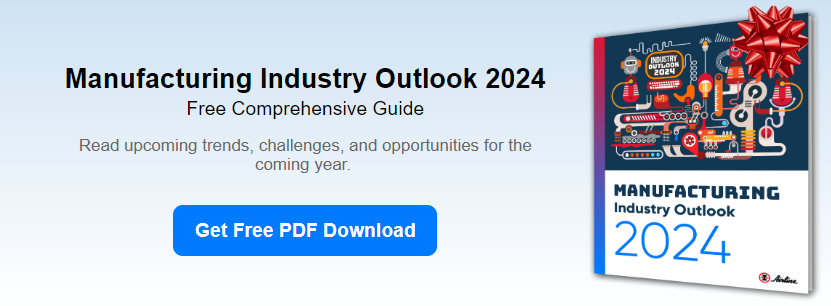
Manufacturing Trends: #1
Production Lines Using Swiss-Army-Knife Systems
One manufacturing trend that continues to grow is the shift from high-volume, low-mix projects to low-volume, high-mix projects. This paradigm shift signifies a significant change in how automation systems are designed and implemented. Instead of being limited to a specific task, these systems are now being developed to handle a broader range of products and processes.
This shift towards greater versatility brings several advantages. Firstly, it allows for quick changeovers between different product variations, enabling manufacturers to respond swiftly to market demands. Additionally, this approach promotes cost efficiency in the long run, as companies can leverage the same automation infrastructure for multiple products, thereby reducing the need for dedicated systems for each specific task.
Pros and cons
Despite the many benefits of moving towards low-volume, high-mix projects, it's worth noting that this transition comes with some potential drawbacks. One significant disadvantage is that low-volume machines may not match their high-volume counterparts' manufacturing output levels. In scenarios where demand is consistently high, manufacturers using low-volume machines may struggle to keep pace. This could lead to missed opportunities, delays in order fulfillment, and potentially dissatisfied customers.
These machines also require more manual interventions for changeovers, potentially increasing labor costs. Manufacturers must allocate resources effectively to accommodate diverse products and processes. This might include training manufacturing employees to handle different tasks and maintaining a robust inventory management system to handle the varying demands.
Furthermore, budget considerations must be carefully managed to ensure that the necessary automation systems and technologies can be implemented without compromising the company's overall financial health. Because low-volume machines are designed for versatility rather than speed, they may not be as efficient in a mass-production model where the same product is made repeatedly.
Balancing these factors against the benefits of greater flexibility is a key consideration for manufacturers adopting this trend. As demands continue to evolve, manufacturing industries are placing high value on nimbleness and quick changeovers to navigate this changing landscape and embrace new opportunities and challenges presented by the shifting needs of customers. By shifting towards low-volume, high-mix projects, manufacturing companies aim to position themselves for success.
Manufacturing Trends: #2
Using Automation to Battle Labor Shortages
Labor shortages have become a significant driving force behind the increased adoption of automation, as companies strive to overcome the challenges posed by the scarcity of skilled workers. This trend is particularly evident in small and medium-sized manufacturers, where automation has evolved from a mere luxury to an absolute necessity.
When implementing these advanced technologies for "smart factories," companies are typically not focused on saving on labor costs. Instead, they are increasingly seeking to reallocate their workforce strategically. By leveraging automation, companies can free up their employees' time and skills to tackle more critical tasks, such as quality control and process improvement. This enhances productivity and ensures that employees can make better use of their expertise and contribute to the organization's overall success.
By embracing automation and creatively reallocating their workforce, manufacturing companies can navigate labor shortages and maximize available resources. This strategic approach addresses the immediate challenges and positions businesses for long-term success in an ever-evolving landscape.
Collaborative Robots
One of the prominent examples is the use of collaborative robots, also known as "cobots." Unlike traditional robots that are kept separate from human workers, cobots are designed to work hand-in-hand with their human counterparts in a shared workspace.
Collaborative robots have sensors, AI, and machine learning capabilities to execute tasks accurately and learn from their interactions. Cobots can perform various tasks, including assembly, pick-and-place, packaging, and quality inspection, alleviating the pressure on the human workforce.
Other examples of automation technologies include autonomous mobile robots (AMRs) for material handling and transportation and computer vision systems for quality control. Such innovative technologies address labor shortages and enhance productivity, quality, and efficiency in the manufacturing process.
Manufacturing Trends: #3
New & Creative Automation Applications
One significant trend is the increased adoption of machine automation by manufacturing companies of all sizes. There has been a remarkable influx of new industries wholeheartedly embracing automation. This surge of "smart manufacturing," at one time, was only for the "big-players" of manufacturing but is now the norm for all.
For some, this has been primarily driven by outsourcing technology services and consultation, as many companies have downsized their internal manufacturing workforce and engineering departments during the pandemic. For others, the availability and affordability of advanced technology (especially when considering their ROI) allow an easier entry point than ever before. The emergence of non-traditional customers and innovative applications for automation is on the rise, opening up exciting possibilities.
A fascinating example of the unconventional use of machine automation is in the agriculture sector, particularly in vineyards. Automation technologies like autonomous robots are being deployed to monitor the health of grapevines. With advanced sensors and AI capabilities, these robots can identify signs of disease or pest infestation on individual plants, enabling early intervention and reducing the need for blanket pesticide use. This not only improves the overall health of the vineyard but also promotes sustainable farming practices. Furthermore, such automation reduces labor-intensive tasks, allowing farmers to focus on other aspects of vineyard management.
Outside the global agricultural robotics market, we see an increasing number of new automation users who now have many opportunities to harness cutting-edge technologies in unconventional processes. For instance, we could witness a broader adoption of mobile robots and AGVs (automated guided vehicles) beyond the traditional confines of warehouse environments. This expansion into diverse sectors promises to revolutionize how automation is utilized and experienced.
Manufacturing Trends: #4
Quickly Accommodating New Customer Needs
In the approaching years, manufacturing companies will experience a heightened need for swift decision-making and execution capabilities. This demand will be driven by customers who expect prompt fulfillment of their requirements.
As technological advancements accelerate, manufacturing organizations face increasing pressure to deliver efficient and rapid solutions. Fostering a culture of innovation and collaboration within the organization can further enhance nimble decision-making and enable companies to adapt quickly to changing market dynamics. Embracing these strategies will empower manufacturing companies to thrive.
Adapting to Customers Going Green
For example, many Original Equipment Manufacturers (OEMs) recognize the growing worldwide demand for sustainable and eco-friendly products. Many of their clients, driven by corporate sustainability initiatives or regulatory pressures, actively seek out "green machines"—manufacturing equipment that minimizes environmental impact through energy efficiency, reduced emissions, or use of sustainable materials.
Just look at the automotive industry. Faced with increasingly stringent emission standards and a customer base keen on sustainability, they strategically decided to transition towards electric vehicles powered by renewable energy sources. This shift reduced the company's carbon footprint and catered to the growing market demand for eco-friendly transportation solutions.
Utilizing advanced technologies such as AI, IoT, and big data analytics, the company optimizes its energy usage during manufacturing. These tech-enabled "green machines" can detect inefficiencies, predict maintenance needs, and improve their own performance over time, leading to significant energy savings and a reduced environmental impact.
This move towards green highlights the importance of manufacturers becoming more agile and responsive to customer demands. By incorporating "green machines" into their offerings, OEMs are playing their part in combating climate change and securing a competitive edge in a market increasingly defined by sustainability. In the face of rising environmental consciousness, moving towards eco-friendly manufacturing designs is a strategic necessity rather than a mere option.
Green initiatives are just one example of how manufacturers are urged by their customers to make necessary improvements, ensuring they stay ahead of the competition and meet evolving market demands. Adapting quickly and effectively will be crucial for continued success.
Manufacturing Trends: #5
Supply Chain Strategies to Mitigate COVID-19's Ripple Effects
The manufacturing sector, in particular, has faced significant challenges in terms of delivery and supply chain disruptions after the COVID-19 crisis. As a result, manufacturing companies have realized the importance of investing in local facilities to mitigate future disruptions. This proactive investment approach, aimed at preventing supply chain interruptions and supporting local economies, contributes to a growing trend known as onshoring.
In fact, many manufacturers are strategically moving towards onshoring and 'near reshoring,' which involves bringing their manufacturing operations back to North America but often in countries like Mexico. This trend is particularly evident in the semiconductor industry, with notable investments being made to support the supply chain in this domain.
However, it's worth noting that macroeconomic uncertainties, such as fluctuating exchange rates and trade policies, may be causing some businesses to hesitate with their reshoring plans. The process of re-shoring often requires making 'Greenfield' investments. These investments entail establishing new facilities, acquiring machinery, and implementing automation strategies. Though the benefits of supply chain resilience are massive, this approach takes time and careful consideration of factors like cost-effectiveness, workforce skills, and long-term sustainability.
Interestingly, we are also witnessing companies that have never previously offshored their operations investing heavily in local equipment, sources of raw materials, and technology. This investment is not necessarily aimed at bringing their production back from overseas, but rather to ensure they can maintain their operations locally and minimize the need to shift their manufacturing activities overseas.
Overall, the ongoing impact of COVID-19 has spurred significant changes in the industry, with automation, supply chain disruptions, reshoring, and the importance of local investments emerging as key themes in response to the challenges posed by the pandemic.
Manufacturing Trends: #6
Evolving Use of Industry 4.0
While many businesses are discussing data and Industry 4.0, the interpretation and usage of these concepts can vary greatly. For instance, when considering two contrasting companies, one may struggle with aspects such as machine connectivity, while the other faces challenges in efficiently monitoring operations from a central location.
Given the wide range of available technologies and the ever-evolving demands of customers, it becomes crucial for businesses to have a clear understanding of their specific needs and how Industry 4.0 technologies can best serve them. By identifying these specific needs and leveraging the right technologies, businesses can effectively navigate the complexities of Industry 4.0.
3D Printing
For example, 3D printing, also known as additive manufacturing, is poised to revolutionize the manufacturing sector. By transforming digital blueprints into tangible objects, 3D printing enables manufacturers to produce complex designs with unparalleled speed and precision. This technology is advantageous for creating custom and small-batch items, eliminating the need for specific tooling or molds.
Furthermore, 3D printing can play a significant role in on-demand manufacturing, whereby products are created only when required, reducing the need for inventory and storage space. This approach aligns with the growing trend toward mass customization, where products are tailored to individual customer specifications.
As 3D printing technology evolves and matures, we will likely witness broader adoption across various manufacturing sectors. From automotive to aerospace, medical to consumer goods, the possibilities are vast and exciting, promising a future of increased efficiency, reduced costs, and enhanced customization.
Manufacturing Trends: #7
Increased Use of Simulation Technology
Virtual reality isn't just a thing of science fiction anymore. It's beginning to play a key role in software, data, and analytics, giving manufacturing companies an edge. For example, augmented reality is making early advancements in maintenance, machine upgrades, and digital twin technology.
What is Digital Twins?
Digital twin refer to a sophisticated concept of creating a digital replica of physical assets, encompassing detailed data models and advanced data analytics, in a virtual environment. The primary objective is to optimize operations by leveraging the power of this digital representation.
However, the true potential of digital twins lies in their ability to provide invaluable insights and inform strategic decisions, ultimately enhancing overall business operations. This transformative technology finds utility in various areas, such as predictive maintenance, ensuring product quality control, and optimizing supply chain management. By harnessing the potential of digital twins, organizations can unlock new dimensions of efficiency and productivity.
As companies increasingly rely on data-driven approaches for decision-making, effectively managing this data becomes crucial. With advancements in machine learning, predictive maintenance, digital twins, and simulation technology, businesses can harness the power of these technologies to drive new levels of productivity.
Manufacturing Trends: #8
Increasing Advancements in Vision
The heightened need for flexibility in systems is being met through advanced vision systems and robotics. These technologies have revolutionized various industries, enabling them to achieve new levels of efficiency and productivity and improved quality control. In recent years, vision systems have made significant advancements, allowing for more precise and accurate automation processes.
For instance, the development of 4D vision and enhanced lighting technology has expanded the capabilities of automation, enabling robots to perceive their surroundings with greater depth and clarity.
What is 4D Vision?
4D vision in manufacturing refers to the cutting-edge vision systems that revolutionize automation. Unlike traditional 3D vision systems that capture spatial data, 4D vision incorporates the element of time, empowering robots with predictive capabilities. Robots can anticipate future states and adapt by understanding an object's location, movement, and changes over time.
This technology proves invaluable in dynamic manufacturing environments where objects are in rapid motion or undergoing changes. The integration of 4D vision significantly enhances the adaptability and efficiency of automated systems, paving the way for more flexible and responsive manufacturing processes.
The continued growth in 4D technology and other improvements in vision systems have opened up new possibilities for automation in complex and dynamic environments. With the continuous progress in these areas, the potential for further advancements and innovations in robotics and vision systems is truly exciting.
Manufacturing Trends: #9
Increased Cloud-Based Digital Architecture
In the modern manufacturing landscape, cloud-based digital architecture is becoming increasingly integral. Cloud computing enables manufacturers to link their operations across different locations, streamlining processes and promoting better data visibility. Not only does it offer scalability and flexibility, but it also allows for more effective collaboration and real-time analytics.
The seamless integration of cloud computing has revolutionized automation systems, empowering companies with remote access and management capabilities. With increasing trust in robust security protocols, global organizations embrace and adopt cloud-based digital architecture for data storage. This strategic move ensures data integrity and unlocks many efficiency benefits vital for global organizations.
The emergence of 5G technology also holds immense potential for the manufacturing industry. With its ultra-fast speeds and low latency, 5G can revolutionize production processes, enabling real-time monitoring, automation, and enhanced connectivity. We are particularly excited about pioneering companies spearheading these groundbreaking developments, leveraging 5G to drive innovation, improve efficiency, and unlock new possibilities in the manufacturing sector. I believe the transformative power of 5G will shape the future of manufacturing, and I can't wait to see the incredible advancements ahead.
Manufacturing Trends: #10
Growing Artificial Intelligence (AI) in the Manufacturing Process
Generative artificial intelligence (AI) has been making waves across various industries, and its impact is no secret. While its potential in the manufacturing sector is still being explored, the possibilities are incredibly impactful. The advancing field of generative AI offers new and exciting opportunities to accelerate automation processes by leveraging existing data.
This valuable data can be utilized to extract detailed engineering designs and comprehensive parts lists effectively, ultimately expediting manufacturing equipment design. By embracing generative AI, manufacturers can unlock greater efficiency and productivity.
For example, General Motors (GM), a prominent manufacturing company, exemplifies the effective utilization of generative design. This automotive giant has partnered with Autodesk, a renowned software company, to harness the power of generative design AI in their production processes. By implementing this technology, General Motors revolutionized the development of innovative vehicle parts, rendering them lighter, stronger, and requiring fewer resources.
GM's generative AI software explores every possible permutation of their parts, considering crucial parameters such as size, weight, strength, and cost. Their result? Remarkable enhancements in fuel efficiency and vehicle performance. This cutting-edge application of generative AI serves as a compelling testament to the immense potential of this technology in revolutionizing manufacturing processes.
With the practical applications of AI and machine learning seamlessly integrated into platforms, industries can unlock new possibilities that were previously unimaginable. The ability to analyze vast amounts of data, make accurate predictions, and automate complex processes revolutionizes various sectors.
However, it is important to acknowledge the challenges associated with integrating different systems within a plant. This requires meticulous planning, coordination, and human checks to ensure a smooth and successful implementation. By addressing these challenges head-on, we see how organizations can harness the full potential of AI and machine learning to drive innovation, improve efficiency, and achieve sustainable growth in 2024 and beyond.
Rest assured, no matter what the future brings, we are here to support you and your company in all areas of fluid power, machine automation, and safety. Together, we can navigate challenges and seize opportunities for growth, innovation, and success in the many years to come.
Get personalized help with all your automation questions and application support. Our experts are always ready to guide you with their knowledge and experience.
- Download our Free 2024 Manufacturing PDF Guidebook
- Blog Post - Manufacturing Automation Software: How to Choose the Right One
- Blog Post - Overall Equipment Efficiency: How to Calculate & Achieve OEE
- Blog Post - From Paper to Pixels: How EDI Revolutionizes Supply Chain Management
- More Automation Blog Posts
Looking ForwardAs we look ahead to 2024 and celebrate Airline's 75th anniversary, we are thrilled to share an exciting collaboration with schools in the Philadelphia area. We firmly believe that future engineers will thrive by embracing their creativity and problem-solving skills. This unique partnership will empower them to become innovative thinkers and leaders, wherever their life takes them. Oh, the places they'll go! |
Leave Comment