Whether it's to become more ecologically friendly, to save valuable space, or reduce overall costs and save on the other green, engineers continue searching for innovations that can shrink hydraulic tank sizes and use less oil. It may surprise you, but the key to oil and tank reduction actually starts with getting rid of something else within your system - Air!
Skip to a section:
Air Is Bad? | How Is Air Getting In? | How Do I Get The Air Out? | Benefits | Summary & resources
Air Is Bad?
- Air causes noticeable pump inefficiency.
- Cavitation effects cause serious damage to components over time.
- Increased temperatures speed the oil's aging process, causing deposits and altering the fluid viscosity.
- Free air increases oil compressibility (makes it more spongy), leading to control issues.
How Does Air Get Into Hydraulic Fluid?
Air can enter hydraulic fluid in many different ways, such as during maintenance, while swapping equipment, from the pump taking in air, leaks, and damaged seals. These sources can be problems, but an inefficient tank is the most significant and most controllable factor bringing air into a system.
Inefficient tanks don't leave enough space for the air and oil to separate from each other properly, and the return oil often sloshes around unnecessarily, creating even more air bubbles. Unfortunately, the smaller the tank size, the less room for air and oil separation, making it difficult to shrink your tank size and use less oil.
How Can I Remove The Air?
To better understand how oil acts in a tank, HYDAC conducted various flow, deaeration, sloshing, thermal, and structural simulations, as well as real-world trials. The results of their research created the Air Separation Return Filter for Tank Optimization, with in-to-out filtration technology.
The oil is directed upstream, flowing from the bottom, forcing air to pass through a special mesh which makes tiny bubbles of air join into larges ones. These larger bubbles then rise to the surface and separate much faster.
The filter outlet also has a unique shape that allows the oil to flow out above the oil surface level, increasing the contact surface between oil and air, letting more air bubbles get separated off. The large outlet surface area also lets the oil flow out at a slower, calmer speed, stopping the creation of new bubbles and giving any existing air bubbles more time to rise to the surface.
|
Tank Optimization Benefits
While initially used in large mobile applications, the filter has been proven beneficial in industrial applications.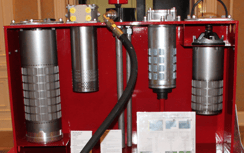
- Improved de-aeration, which increases machine reliability.
- Oil volume reduction saves costs and is environmentally friendly.
- Tank size reduction saves material costs and frees up space for other components.
- Simplifies tank fittings and connections, which saves material and hassle.
- A variety of mounting options (shown right) to optimize your tank's capabilities fully.
- Oil aging and steering problems were significantly reduced.
Summary
To reduce your system's oil volume and tank size, you first have to solve the problem of having adequate air and oil separation, which often means using a larger tank. HYDAC's Air Separation Return Filter for Tank Optimization helps deaerate the oil in your system in two ways. By forcing tiny air bubbles through a mesh that joins them for easier removal and preventing new air bubbles from forming by having a slower oil flow from the top of the oil, providing more contact surface area. Combined, these two benefits allow for significantly less air in your system, which reduces cavitation damage, oil aging, efficiency losses, and steering problems, and allows for a smaller tank and less oil.
If you have any questions about optimizing your hydraulic system, contact one of our industrial experts, who would be happy to help!
Related Articles & Resources
PDF brochure: Air Separation Return Filter for Tank Optimization
Explore more hydraulic Technically Speaking articles
Leave Comment