-
Today's manufacturing systems wouldn't have the best productivity or efficiency without presence sensors. This blog will review the most widespread presence sensors used in factory automation designs so you can decide which is best for your application.
Skip to a section:
Presence sensors | Inductive proximity sensors | Capacitive proximity sensors | Magnetic proximity sensors | Photoelectric sensors | Diffuse photoelectric sensors | Through-beam photoelectric sensors | Retroreflective photoelectric sensors | Laser distance sensors | Fiber optic sensors | Ultrasonic sensors | Limit switches
What are presence sensors?
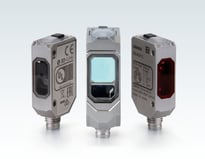
Presence sensors detect the distance, absence, or presence of an object, often referred to as the target. Presence sensors are aptly named because they detect the "presence" of the target. There are many types of presence sensors. We will focus on five of the most popular categories of presence sensors: Proximity sensors, photoelectric sensors, fiber optic sensors, ultrasonic sensors, and limit switches.
If you have questions or need help with choosing a suitable presence sensor for your application, you can always reach out to Airline's industrial automation product experts, who are ready to help.
1. Proximity Sensors
What are proximity sensors?
Proximity sensors are one of the original types of sensors created. They are rigid, dependable, and repeatable non-contact sensors that transmit data about the presence or motion of a target into an electrical signal. They output an ON signal when the object enters their sensing range. Proximity sensors are split into three main categories, inductive proximity sensors, capacitive proximity sensors, and magnetic proximity sensors.
What are inductive proximity sensors?
Inductive proximity sensors are used to detect metal targets without coming into contact with the target. How do inductive proximity sensors work? By creating an inductive field around the end of the sensor, so when a ferrous metal approaches, the sensor triggers an output on the sensor. Non-metallic substances, such as dirt and liquid, do not interfere with the detection, so an inductive proximity sensor can effectively operate in wet or dirty conditions.
The cons to this technology are the sensing distance. The sensing distance varies by the target's metal composition but typically max out at two to three inches away. Some considerations before using these (or any sensor) are the distance to the target, the material of the target, if the sensor needs to be embedded into a workpiece, the required output type, and other application specifics.
What are capacitive proximity sensors?
Capacitive proximity sensors (CPS) are non-contact devices designed to detect both metallic and non-metallic targets but are ideally suited for plastic, wood, and other non-metallic targets, for liquid level control, and for sensing powdered or granulated materials. A capacitive proximity sensor gets its name because it uses dielectric principles of capacitance to establish its sensing field.
What are magnetic proximity sensors?
Magnetic proximity sensors are non-contact devices that detect targets beyond the normal limits of inductive sensors. They usually have a mating magnet mounted to the target, and once the sensor detects the presence of the paired magnet, the output will change, and the target will be detected. This sensor works great for applications like verifying door closures. They come in many shapes and sizes and can detect magnets through walls of non-ferrous metals, stainless steel, aluminum, plastic, and wood.
2. Photoelectric Sensors
What are photoelectric sensors?
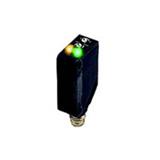
Photoelectric sensors are relatively inexpensive and can be used in almost any application, making them one of the most popular presence sensors used today. They use LED or Laser technology to emit a light beam (visible or infrared) from its light-emitting element to detect the presence of a target. There are four types of photoelectric sensors: Diffuse photoelectric sensors, through-beam photoelectric sensors, retroreflective photoelectric sensors, and laser distance sensors.
What are diffuse photoelectric sensors?
Diffuse photoelectric sensors detect targets by sending out a light beam, and the intended target will reflect this light beam to a receiving element on the sensor. Before using a diffuse photoelectric sensor, things to consider are the target's color, sheen, and shape, which affect how light will bounce from the target. For example, the darker the target's color, the shorter the sensor's effective distance will be. The pros of diffuse photoelectric sensors are they're very cost-effective and installed at only one point on the system. The cons are they can sometimes be less accurate than through-beam or reflective sensors.
![]() |
Watch a quick demonstration of Omron's E3AS-F Time of Flight Sensor and read about more useful specs and information! |
What are through-beam photoelectric sensors?
Through-beam photoelectric sensors require two devices, an emitter sending out a light beam and a receiver accepting that beam to complete the light circuit. The output will change if a target object breaks that beam. The advantages of through-beam sensors are they can be used over long distances and are very accurate and dependable. For example, a through-beam sensor can detect objects more than 10 m away, a feat impossible with magnetic, ultrasonic, or any other sensors. The downsides are that you must install both an emitter and receiver at two different points on the system, and may not function correctly with translucent targets.
What are retroreflective photoelectric sensors?
Retroreflective photoelectric sensors are a hybrid between through-beam photoelectric sensors and diffuse photoelectric sensors, Retroreflective sensors send a light beam to hit a separate reflector to send the light back to the sensor. The sensor detects that a target is present if an object breaks the light beam between the reflector and the sensor. The appeal to retroreflective sensors is that you can have a through-beam sensor's accuracy, and since the reflector is a static device, it does not require a power source. The downside is retroreflective sensors have a shorter range than through-beam sensors.
What are laser distance sensors?
Laser distance sensors are designed for non-contact distance measurements. Laser distance sensors work based on the Time-Of-Flight (ToF) principle by emitting a laser beam and detecting how long the return pulse takes. The sensor can use that measurement to calculate the distance from the target. Applications for these include height profiling objects and warning of approaching objects.
3. Fiber Optic Sensors
What are fiber optic sensors?
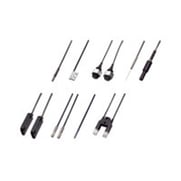
Fiber optic sensors are devices that use photoelectric technology through fiber optic cables to get sensing beams into very tight spaces. These reliable sensors are commonly used for remote detection in narrow places or other locations with limited access. Fiber-optic sensors are also immune to electromagnetic interference and do not conduct electricity, so they can be used in places with high-voltage electricity or flammable materials. They can also be designed to withstand high temperatures as well.
4. Ultrasonic Sensors
What are ultrasonic sensors?
Ultrasonic sensors detect targets by sending out a sound pulse, and similarly to photoelectric technology when that sound pulse is reflected off the target and back to the sensor, it generates an electrical signal. Ultrasonic sensors can be configured to change output states based on the time it takes to sense the return pulse. Ultrasonic sensors have two main components: the transmitter, which emits the sound, and the receiver, which get the sound after it has traveled to and from the target.
The plus side to ultrasonic sensors is their immunity to any color/sheen differences of the target, making them excellent for detecting transparent targets, such as transparent films, glass bottles, plastic bottles, and plate glass. However, you must consider the target object's size and shape, as smaller targets can be difficult to sense.
5. Limit Switches
What are limit switches?
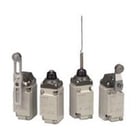
Limit switches are the original sensor used to detect the presence or absence of an object. This sensor requires physical contact with the target to engage an output contact, similar to how you open up a refrigerator door and the light turns on inside. Pros include these sensors' durability and dependability, Cons are that these sensors have a shorter life span when compared to other technologies due to mechanical wear.
Summary
Presence sensing is a fundamental building block of any industrial automation system. These devices are used to detect the presence of an object, the end of travel on a workpiece, and even the height of an object. There are many types of presence sensors, and their functions can differ. Today's blog covered factory automation systems' five most popular sensing devices.
If you have any questions about which devices are best suited for your industrial automation applications, reach out to our product experts, or you can shop for the listed products below.
Related Articles & Resources
Industrial Automation Articles
Omron's Time of Flight Sensor Tech | Can You Sense That?
Shop sensors
Contact an expert for sensor selection
Leave Comment