Rockefeller University in Manhattan wanted to expand its campus, but the cramped city space forced them to think outside the box. Utilizing their air rights, they planned an ambitious expansion directly overtop of F.D.R. Drive, a busy, multi-lane highway.
Leading to build time, one key question remained; How do you keep nineteen, 400 ton, pre-built structures completely level, while transporting them over the East River and into position? Well, that's why Federated Crane called Airline.
Jump To Section:
The Task At Hand
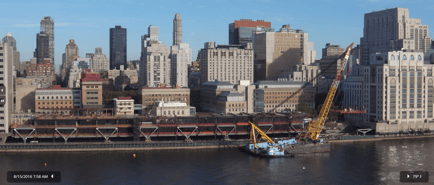
This project was anything but ordinary. The 500 million dollar project looked to add two building stories, with two acres of space on the roof, all straddling the highway. There was almost no precedent for a build like this, something this scale was only done once before, a long time ago, with everything done manually.
To reduce traffic issues, engineers decided the best plan of attack would be to prefabricate the build's 50-foot-wide structures in Keasbey, New Jersey, and then transport them down the East River on barges. There are only two floating cranes in the entire United States that could lift the 800,000-pound structures, with the heaviest piece for the project weighing 1.5 million pounds! The Chesapeake 1000, the largest crane on the East Coast, did the heavy lifting, but the question remained; how do we keep these massive structures level while they're being lifted in and out of position?
Getting The Call
Federated Crane was contracted to supply that answer. Since the early 2000s, Airline and Federated Crane have worked on multiple "big builds" together, all requiring various custom applications, like diesel power units, control panels, supply jacking cylinders, and more. That's why when Federated needed hydraulic and control experts they could trust, they called Airline.
A Pivotal Role
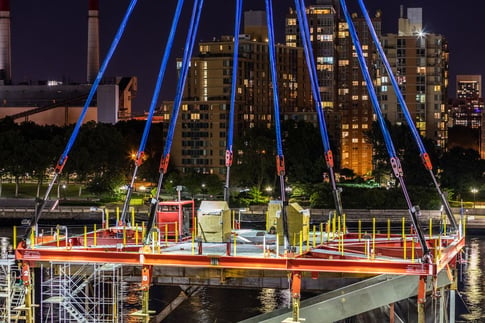
So, how did we do it? Our hydraulics and controls experts helped build this system to adapt to each structure's different center of gravity, and formulated separate "recipes" or specifications for each lift. There was no room for error; the slightest miscalculation would lead to the structure's weight destroying itself. Using fluid power, each arm, or cylinder (shown right), could detect its length and the weight it was holding, and manipulate itself accordingly, ensuring the level lift of all nineteen different 400-ton structures.
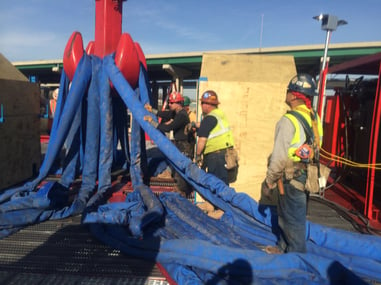
The first time they built to this scale, each arm was manually operated, and that person would adjust their cylinder length during the lift. It was extremely dangerous, which is why something of this scale wasn't done again. Until now, that is. Thanks to modern technology, this system was able to be remotely controlled, operated, and monitored. This massive build only took Airline four months to complete successfully!
The Key To The Operation
Projects like these don't succeed without flexibility, and that's where having a wide array of lines to build with was vital. So along with the hydraulics and controls expertise our engineers provided, we utilized more than five different manufacturers in the final package, providing a completely custom offering.
- FABCO: Custom-built generators.
- HYDAC: Custom-designed cylinders.
- Bosch Rexroth: VT-HACD control cards.
- Omron: Controller NJ series of products (The brains of the operation).
- Phoenix Contact - Terminal blocks for reducing generation vibration.
Being flexible came in handy on-site as well. During the project, it came to attention that there was no remote emergency shut-off in the original design, only a manual. That's not safe, so our experts sprung to action and modified on-site, creating a remote kill switch for the client, leading to less downtime and no delays.
Summary
This build was indeed a marvel in engineering, and not one for the faint of heart. With only four months to deliver mission-critical components and controls, Airline ensured that each of the massive structures could get put into place in one piece. While we only had a small (but key!) role in this project overall, we are proud to have had the opportunity to support Federated Crane and the entire Rockefeller University expansion project in this historic build.
If you need hydraulics or controls assistance for projects big or small, Airline Hydraulics has experts ready to help!
Resources and Information
- New York Times Article:
Rockefeller University Starts Its Expansion Over a Busy Highway
- Technically Speaking Blog
Contact Us!
Ask your Airline Rep. or contact us for assistance with ordering or customizing an order.
- 800-999-7378
Leave Comment